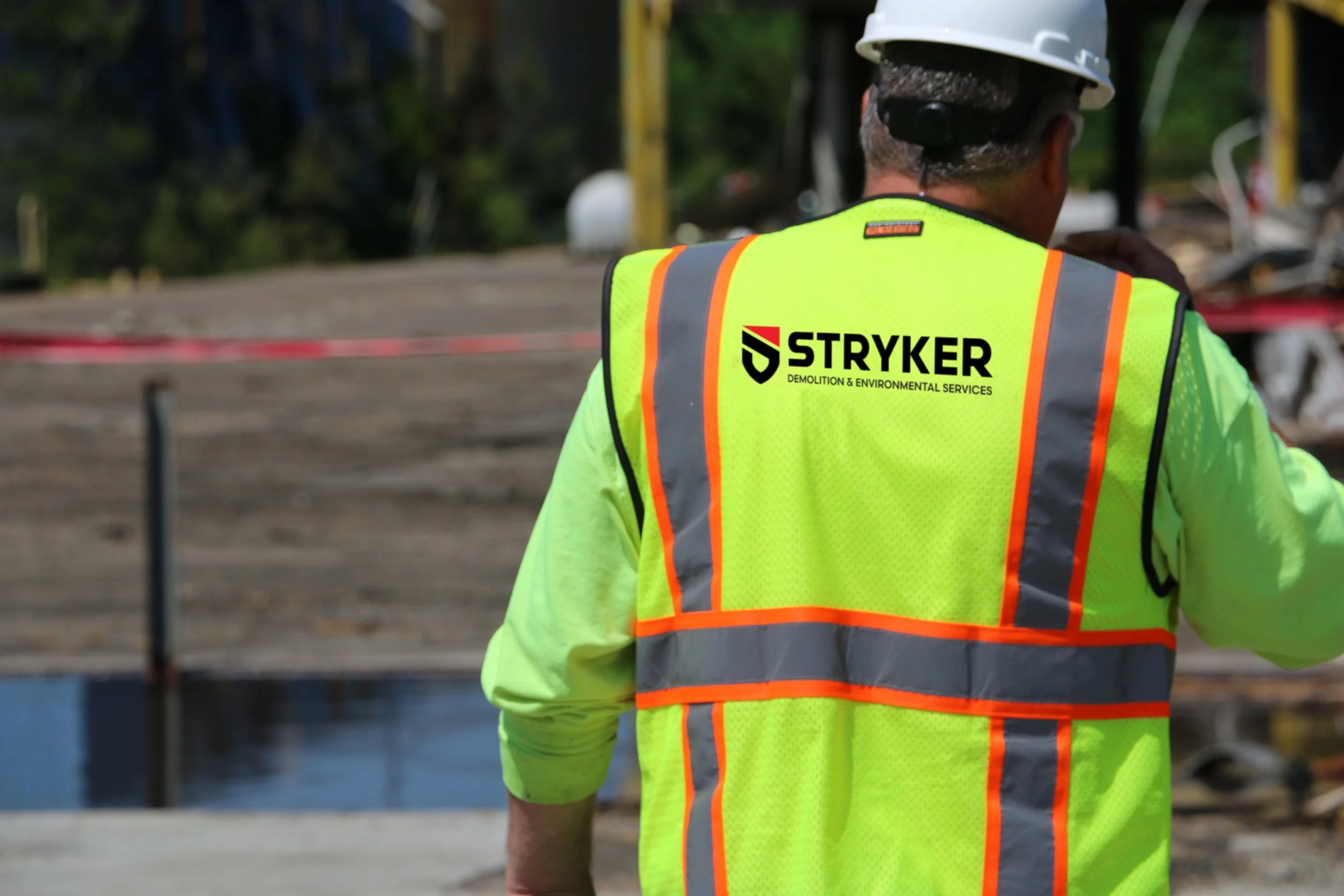
HEALTH
& SAFETY
At Stryker Demolition & Environmental Services, our commitment to health and safety is paramount—not just a standard practice, but a cornerstone of our operational philosophy. We dedicate ourselves to maintaining a secure and healthy work environment for our employees, clients, and the general public. To achieve this, we implement rigorous onsite processes and controls that are regularly reviewed and updated to ensure compliance with local, state, and federal regulations.
From the moment our associates join us, they receive comprehensive safety training and certifications that continue throughout their tenure to keep safety practices sharp and effective. Each project is guided by a site-specific Health and Safety Plan (HASP) and detailed Work Plans, which are actively reinforced through daily morning safety meetings. This proactive approach ensures that safety is always at the forefront of our operations, reflecting our commitment to protecting all stakeholders involved in or affected by our projects.
Stryker DES is a pre-qualified contractor by Avetta, ISNetworld, Veriforce
& is a member of the National Demolition Association.
Employee Core Training
Stryker DES New Hire Training and Safety Orientation
OSHA 10-hour site worker
OSHA 30-hour site supervisor
OSHA 40-hour HAZWOPER
CPR/First Aid/AED/Blood-bourne Pathogen
Asbestos Handler and Supervisor
Lead Handler and Supervisor
Respiratory Protection/PPE
Fall Protection
Hazard Communication
Confined Space Entry
Fire Prevention (PASS)
Scissor and Aerial Lift
Powered Industrial Truck
Electrical Safety
Lockout/Tagout
Scaffold
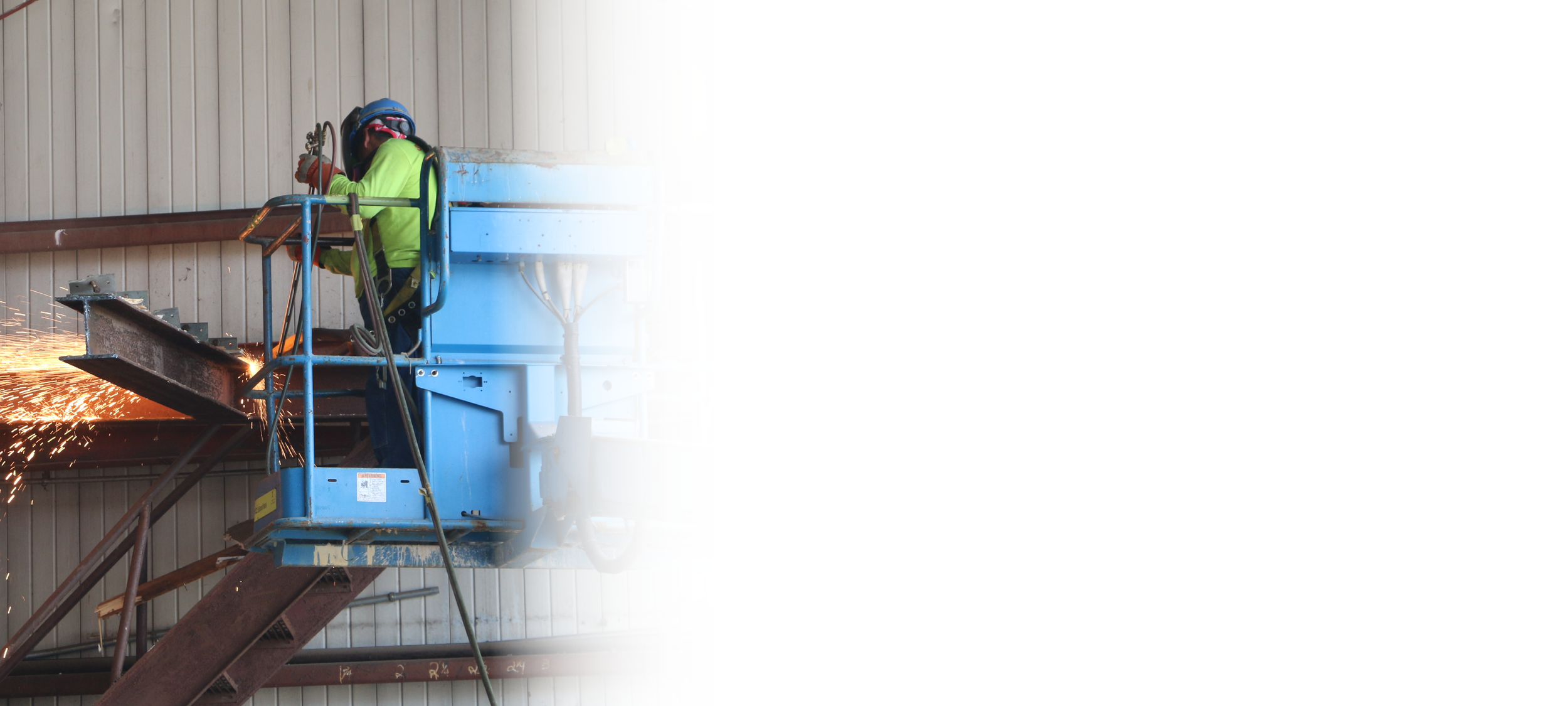
Safety at Stryker DES is not just about compliance; it's a culture.
We foster an environment where safety is everyone's responsibility, encouraging open communication and continuous improvement.
Our safety culture is supported by:
Regular Safety Audits and Inspections – Ensuring ongoing adherence to safety protocols and identifying areas for improvement.
Employee Safety Committees – Involving employees in safety discussions and decisions to enhance engagement and compliance.
Continuous Learning Opportunities – Providing ongoing education on the latest safety innovations and best practices.
Reward and Recognition Programs – Acknowledging and rewarding employees for exemplary safety practices.
By continuously striving to improve our safety practices, we not only comply with industry standards but set new benchmarks for safety and operational excellence in the demolition and remediation industry.